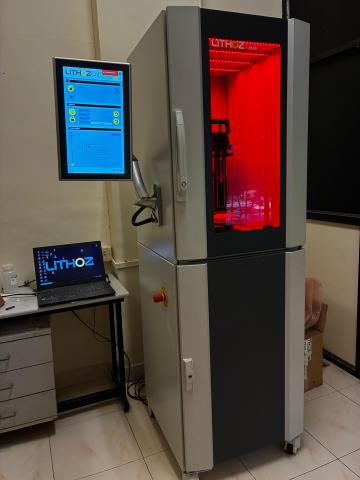
External users: registration to be carried out only through I-STEM portal
Additional information about sample and analysis details should be filled in the pdf form provided in the I-STEM portal under “DOWNLOAD CSRF”
Internal users (IITB): registration to be carried out only through DRONA portal
Additional information about sample and analysis details should be filled in the pdf form provided here.
.
Category
- Fabrication and Processing » Microfabrication
Booking Details
Facility Management Team and Location
Facility Features, Working Principle and Specifications
Digital Light Projection (DLP)-based ceramic additive manufacturing is a high-resolution 3D printing technique that enables the fabrication of complex ceramic components through photopolymerization. The process begins with the preparation of a ceramic slurry, which consists of finely dispersed ceramic powders (such as alumina, zirconia, or silicon carbide) mixed with a photosensitive resin containing photoinitiators and additives for stability and flow. This slurry is selectively cured layer by layer using projected ultraviolet (UV) light patterns from a Digital Micromirror Device (DMD), which corresponds to the cross-sections of a 3D CAD model. Each exposed layer solidifies, forming the “green part” composed of ceramic particles bound in a polymer matrix.
After printing, the green part undergoes thermal debonding (debinding) to remove the organic resin and binders. This step involves slow, controlled heating to prevent internal stresses, cracking, or deformation, resulting in a porous "brown body" with low mechanical strength.
The final step is sintering, where the debound part is heated to high temperatures to fuse the ceramic particles together. This densification process strengthens the structure and reduces porosity, producing a mechanically robust final ceramic component. Sintering also causes shrinkage, which must be accounted for during the design phase.
Overall, DLP-based ceramic additive manufacturing combines high accuracy, surface quality, and design flexibility, making it suitable for producing intricate ceramic parts in fields like biomedical engineering, aerospace, electronics, and advanced structural applications. It enables rapid prototyping and small-scale production of ceramics with complex geometries not achievable through traditional methods.
Present facility is for printing only.
Sample Preparation, User Instructions and Precautionary Measures
CAD Model
Charges for Analytical Services in Different Categories
X = 400 Rs/Hour for 3d printing | |
Charging Method | |
Category | User Charges (Suggested by Committee) |
IITB TAs on specific Instruments | X/2 |
IIT Bombay | X |
Other Academic Institutes | 2 X + 18% GST |
National Labs | 4 X* + 18% GST |
Industries | 5 X* + 18% GST |
Start-up (SINE incubation) | 4 X + 18% GST |
Monash IITB | X + 18 % GST |
SAARCS countries and African Counties (Low-Income Countries) | Academic 5 X, Industries 10 X |
For Other Countries | Academic 10 X, Industries 20 X |
1. Printing Time and Material weight will be decided by machine software as per the CAD Model |
2. Users have to pay separate for the material (Material Rate as per Lithoz) |
3. As per recommendations, only Lithoz material is recommended on machine |
Applications
- Aerospace
Biomedical
Sample Details
SOP, Lab Policies and Other Details
Publications
- Reddy, Pranith Kumar, Prasanna Gandhi, and Gurminder Singh. "Additive manufacturing of yttria-stabilized zirconia using digital light processing: Green density and surface roughness analysis." Ceramics International 50, no. 13 (2024): 22974-22988.
- Puchakayla, Pranith Kumar Reddy, Bhaskar Pegu, Prasanna Gandhi, and Gurminder Singh. "Defects evolution during printing, debinding and sintering for additive manufacturing of yttria stabilized zirconia." Materials Characterization (2025): 114752.